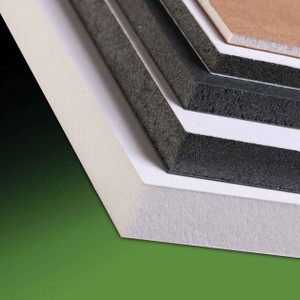
GP APEX™ High-Performance Foam Board - Next Generation Plastic-Faced Substrate for Premium Display Applications
GP APEX™ is the latest innovation in 3A Composites’ high-performance foam board portfolio, featuring an extruded polystyrene core laminated with high-impact polystyrene facers using advanced adhesive technology. The result is an exceptionally flat, rigid substrate optimized for digital printing, vinyl application, and durable display use.
Designed for today’s demanding digital print workflows, GP APEX™ offers vibrant color reproduction, superior consistency, moisture resistance, and repositionable vinyl compatibility—everything needed for premium display applications that require both visual impact and structural performance.
How Does GP APEX™ Compare to Other Plastic-Faced Foam Boards?
- Enhanced Flatness: Proprietary process controls yield exceptional sheet flatness critical for precise digital printing.
- Advanced Adhesive Technology: Stronger bond between core and facers minimizes delamination and edge fraying.
- Improved Color Reproduction: Engineered surface maximizes vibrancy and image sharpness.
- Superior Consistency: Tight manufacturing tolerances ensure uniform thickness and performance.
- Fabrication Ease: Cleaner cuts and routing with reduced debris and material waste.
Features & Benefits
- Exceptional Flatness: Eliminates surface waves for flawless print and mounting results.
- Vibrant Color Reproduction: Smooth HIPS facers optimize digital UV and direct-to-substrate printing.
- Superior Rigidity: Combines lightweight foam core with high-impact facers for structural strength.
- Moisture Resistance: All-plastic construction withstands humidity and occasional water exposure.
- Fabrication Performance: Advanced lamination reduces edge fraying in cutting, routing, and finishing.
- Vinyl Compatibility: Facers support repositionable vinyl graphics without surface damage.
- Warp Resistance: Balanced construction maintains flatness in varied environments.
- Consistent Quality: Uniform sheet-to-sheet performance through enhanced process control.
- Made in the USA: Produced in 3A Composites’ domestic facilities under strict quality standards.
- GATOR® Family Heritage: Builds on decades of performance from the trusted GATOR® lineup.
Technical Specifications
Specification | Details |
---|---|
Core Material | Extruded polystyrene foam |
Facer Material | High-impact polystyrene (HIPS) |
Bonding Method | Advanced adhesive lamination technology |
Available Colors | White (standard), black (special order) |
Surface Finish | Smooth, low-gloss |
Standard Thicknesses | 3/16″ (4.8 mm), 1/2″ (12.7 mm) |
Standard Sheet Sizes | 48″×96″, 60″×120″ |
Weight | Lightweight (varies by thickness) |
Edge Properties | Clean cuts with reduced fraying |
Print Compatibility | Digital UV, screen, vinyl, direct-to-substrate |
Water Resistance | Excellent |
Cutting Methods | Knife, saw, router, CNC |
Applications
- High-End Digital Printing: Optimized for modern UV and direct-to-substrate printers, delivering photo-quality images with vibrant color.
- Retail Signage & Displays: Flat, consistent panels for department stores, point-of-purchase, and branded retail environments.
- Exhibition & Trade Shows: Lightweight yet durable graphics that maintain impact over multi-day events and frequent handling.
- Interior Wayfinding: Stable substrates for clear, long-lasting directional signage in corporate, healthcare, and educational facilities.
- Vinyl Graphics: Surface supports repositionable vinyl for changeable messaging and precise installation.
- Museums & Galleries: Premium informational displays that complement exhibits with exceptional visual quality.
Printing & Fabrication Capabilities
Printing Options
- Digital UV Printing: Exceptional adhesion and color vibrancy on ultra-flat HIPS facers.
- Screen Printing: Stable surface for accurate registration and vibrant spot colors.
- Vinyl Application: Facers allow repositioning without substrate damage.
- Direct-to-Substrate: Compatible with flatbed printers using various ink systems.
Fabrication Techniques
- Cutting: Knife, sawing, routing, and CNC with minimal fraying.
- Routing: Precision profiles and dimensional elements with clean edges.
- Die Cutting: Accurate shapes with consistent edge quality.
- Mounting: Adhesives and mechanical fasteners for wall or multi-layer displays.
The GATOR® Family: Find Your Ideal Board
GP APEX™
- Extreme flatness
- Vibrant digital print performance
- Reduced edge fray
GATORPLAST®
- Moisture resistance
- Vinyl graphic capability
- Smooth plastic facers
GATORFOAM®
- Wood-fiber veneer facers
- Maximum rigidity
- Dent resistance
GATORFOAM® PRO
- Enhanced print surface
- Static resistance
- Superior ink adhesion
Installation & Handling Recommendations
Storage & Handling
- Flat Storage: Protect flatness by storing sheets level with full support.
- Temperature: Acclimate 24 hours before use; avoid extremes.
- Protective Film: Remove just before printing or fabrication.
Mounting & Cutting
- Adhesives: Use polystyrene‑compatible adhesives; test solvent-based first.
- Edge Finishing: Band or paint for premium exposed edges.
- Fasteners: Pre-drill oversized holes for thermal expansion.
Printing Tips
- Surface Prep: Ensure clean, dust‑free substrate.
- Printer Settings: Optimize for plastic substrates per manufacturer guidance.
- Curing: Balance UV cure to avoid overheating and warping.
Frequently Asked Questions About GP APEX™
What makes GP APEX™ different from standard boards?
Can GP APEX™ be used outdoors?
Which printing methods excel?
How does it handle cutting?
Elevate Your Digital Printing Projects with GP APEX™
When you need unmatched flatness, color vibrancy, and fabrication ease, GP APEX™ delivers next-generation performance for your most demanding display applications.
Contact your Laird Plastics representative today to learn how GP APEX™ can transform your premium graphic displays.